WE SHARE OUR KNOWLEDGE
January 16 2025
Digital transformation in manufacturing: why is Comarch IoT MES a must-have?
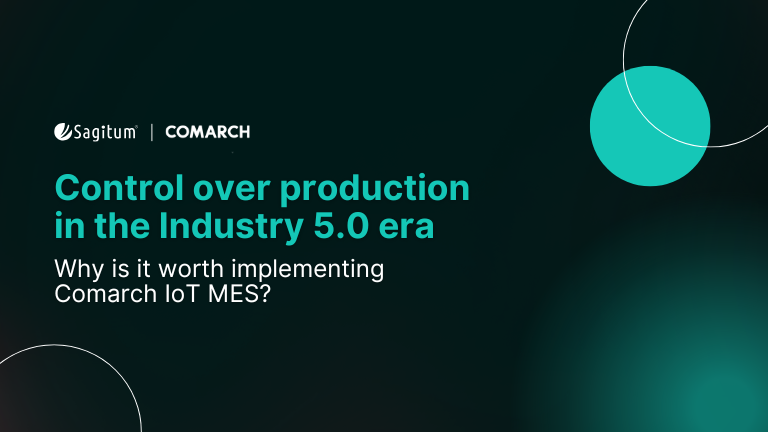
Industry 5.0, leveraging advanced tools of digitization, automation, and the Internet of Things (IoT), is transforming traditional manufacturing plants into intelligent factories of the future. Modern businesses are focusing on solutions that not only streamline operational processes but also enable faster responses to changing market demands. Thanks to cutting-edge production management systems like Comarch IoT MES, companies gain full control over their processes, optimize production, and maximize efficiency – all based on real-time data.
Comarch IoT MES is a solution designed for real-time monitoring and management of production processes. It integrates IoT technologies, enabling the automatic collection of data from machines and production equipment, allowing for continuous tracking of production parameters, identification of issues, and process optimization. With Comarch IoT MES, companies can increase efficiency, minimize downtime, and respond more effectively to changing production conditions.
In which industries will the Comarch IoT MES solution be effective?
Comarch IoT MES is a solution that can bring significant benefits across many industries, especially where precision, automation, and effective management of production processes are crucial. With advanced features such as machine integration, real-time production monitoring, and quality control, this system is perfectly tailored to the specific needs of many industrial sectors.
These include, among others:
- Manufacturing companies – mechanical (metalworking, assembly), plastics, FMCG (production, packaging), suppliers, Automotive Tier 1&2
- Wood processing
- Chemical industry
- Textile industry
- Food industry
Why Comarch IoT MES?
- Integration with ERP systems
Comarch IoT MES seamlessly integrates with ERP systems, such as Comarch ERP, enabling data synchronization across various processes within the company. This ensures that all information related to production, inventory, orders, and resource management is available in one place. Such integration allows for better production planning and provides full process transparency, enabling quicker decision-making and more efficient management of the entire organization.
- Automatic and manual work declaration
The Comarch IoT MES system allows both automatic and manual work declarations for individual production stations. Automatic declarations are generated based on data from machines and sensors, minimizing the risk of human error. On the other hand, manual declarations allow operators to input additional information that may be crucial for analyzing the production process.
- Production traceability
The system records and stores all data related to each stage of production, enabling a full trace of the product’s history. This allows companies to track the origin of raw materials, specific operations, and every change made during production. Traceability is particularly important in industries where quality and regulatory compliance are crucial.
- Quality control
Comarch IoT MES supports quality control at every stage of production. Through integration with sensors and machines, the system continuously monitors process parameters, allowing deviations from standards to be detected and corrected immediately.
- Preventive maintenance
The system enables early detection of potential issues with machines and equipment through the analysis of sensor data and automatic monitoring of technical conditions. Comarch IoT MES supports preventive maintenance, helping to prevent failures and minimize downtime by planning repairs before breakdowns occur.
- Real-time production monitoring
This feature gives managers and operators full visibility into what is happening on the production floor, enabling quick responses to any irregularities or downtime. The system provides information on production progress, machine efficiency, and operator performance, allowing for real-time operational decision-making.
- Automatic and manual downtime declaration
The Comarch IoT MES system allows the recording of production downtime both automatically, based on data from machines, and manually, when operators report unplanned breaks in production. This enables companies to analyze the causes of downtime, leading to better production management and minimizing losses due to idle time.
- Historical data recording for reporting
Comarch IoT MES collects all production data, which can be stored in the system and used for generating reports. Recording historical data allows for the analysis of production efficiency, identification of trends, and optimization of processes.
- Integration with machines and sensors
The system allows full integration with machines and sensors, enabling automatic data collection directly from production devices. This ensures that all information about machine status, energy consumption, and process parameters is available in real time. This automation reduces errors and allows for more precise production management.
The path to intelligent manufacturing – key features of Comarch IoT MES
Production panel for operators
The panel displays essential information about ongoing production orders and operations, including the current OEE (Overall Equipment Effectiveness) indicator.
Andon boards
Andon boards are electronic displays used in manufacturing plants to visualize key indicators related to process progress. They allow employees to monitor critical parameters in real-time, making it easier to quickly identify problems and make decisions.
Maintenance
The maintenance module allows for the assignment of regular service tasks to each machine, defining their frequency and calculating the required man-hours for their execution.
The current service status is visible both on the production panel and in the office part of the system. Employees receive notifications reminding them of the need to perform scheduled maintenance tasks.
Production materials control
Integration with the ERP system allows for tracking and controlling the materials used. The employee can display a list assigned to the current operation and declare the consumption of individual materials and products.
Machine monitoring
The system enables efficient analysis of workstation performance to improve machine availability. Additionally, the solution provides information on the number of micro-downtime reports, helping to eliminate the most frequent incidents.